 |
Room Temperature Curing, One-Part Silicone Rubbers |
 |
 1
Materials, Chemicals, Time Needed |
 |
- Scotch tape, pH indicator paper, spatula, water-color paints
+ brush
- 3 U-shaped profiles or matchboxes
- 3 thermometers
- WACKER Silicon ELASTOSIL® E43, Xi, F, N
- WACKER Silicon ELASTOSIL® N199, Xi, F, N
- Calcium sulfate
Allow about 20 minutes to prepare the samples. The experiment
will take around 40 minutes overall. The samples will need
approx. 1 day to fully cure.
|
 |
 2
Procedure and Observations |
 |
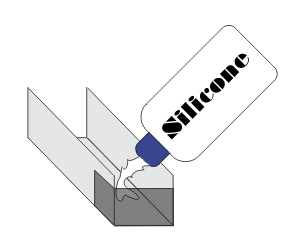 |
 |
Cover
the ends of two U-shaped profiles with adhesive tape.
Fill
one with ELASTOSIL® E43 and press the
compound down with a wet finger. Do the same with the
second profile,
using ELASTOSIL® N199.
Fill the third
profile with gypsum, and scrape off the excess with
a spatula. If no profiles are available, use empty matchboxes.
Place
a thermometer in each sealant, and place a moistened strip of
pH indicator paper on the edge of the profile (see Photo
1). |
|
Fig.: 1 Filling a
U-profile with sealant |
 |
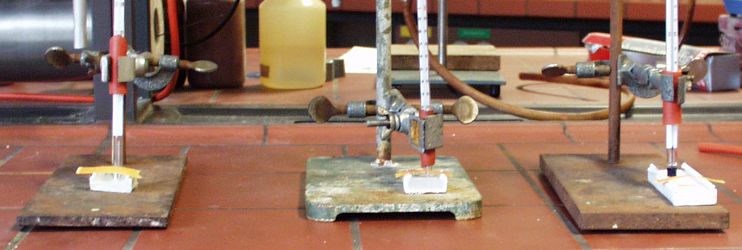 |
Photo 1: Experimental
set-up |
|
|
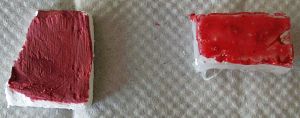 |
 |
During
the experiment, monitor the temperature and the change
in odor
of each sealant for about 1 hour and tabulate the results.
After
final curing, check the samples for impact strength,
consistency and ease of overpainting with water-colors
(see Photo 2). |
|
Photo 2: Gypsum and silicone sample after painting
with water-color |
 |
Tabulate these results as well. The following
observations were made when the experiment was repeated several
times: |
 |
|
 |
Measurements taken as the samples
were curing revealed that the temperature of all three samples
rose by around 1.5 °C. |
 |
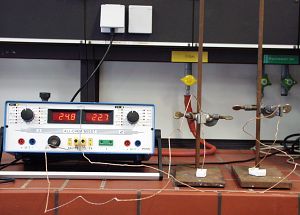 |
 |
The
temperature changes plotted in the adjacent diagram
were measured with the "All-Chem-Misst" classroom
instrument and dedicated software (see Photo 3).
The measurements are mainly intended to reflect the
change in temperature. As gypsum cures, the temperature
rises sharply at first and then drops continually
until it remains almost constant (see diagram). In
contrast, the temperatures of the silicones changed
by different amounts and followed no particular pattern
(see diagram). |
Photo 3: Setup for "All-Chem-Misst" measurements |
|
|
 |
 |
 |
|
|
 |
|
 |
 3
Discussion of Results
|
 |
The test observations (see Table
1) reveal clear differences between gypsum and the two RTV-1
silicone rubbers. The two silicone rubbers cure by reacting in
several stages with the moisture in the air to form elastomers
(see Part 5 Supplementary Information). The cured material has
a soft, rubbery consistency and is elastic.
The acrid odor and the acidity of ELASTOSILS ® E43
stem from the fact that this system contains an acetoxy-based crosslinker
that releases acetic acid during the first hydrolytic reaction
step.
ELASTOSIL® N199, in contrast, is a neutral system. Water-colors
adhere poorly to silicones and can be easily washed off because silicones
are highly water repellent and have a non-stick effect (see also the following
experiments: "Water-repellent properties of
silicone fluids", "Silicones
in masonry protection" and "Silicone-coated
paper").
When gypsum cures, water molecules are incorporated into the ionic lattice
of the calcium sulfate. The calcium sulfate CaSO4 is thereby
converted into calciumsulfate dihydrate (gypsum) CaSO4 · 2
H2O. Because gypsum is an ionic compound, it is brittle and
breaks when subjected to mechanical force, such as a hammer blow.
The observed change in temperature accompanying the curing of gypsum may
be explained as follows: The temperature rise is due to Coulombic forces
between the water dipoles that penetrate into the ionic lattice and ions.
Some of the heat released is needed for evaporating the excess water. The
rest of the heat escapes to the surroundings. As a result, the gypsum cools
down.
The differences observed in the temperature changes accompanying curing
of the silicone rubber are the manifestation of several exothermic and
endothermic processes. These vary in nature and extent with the materials
employed and the method of preparation. Hydrolysis of the side groups (e.g.
acetoxy groups) and condensation of the silanols are exothermic reactions
whereas evaporation of the by-products (e.g. acetic acid) are endothermic
reactions. This leads to totally different, non-uniform temperature changes.
The properties we have just observed indicate that gypsum would not make
a good jointing material for joints subject to movement and stress due
to the fact that it is not elastic. It is suitable, however, for purely
decorative joints that involve no movement and are likely to be painted.
As for the two RTV-1 silicone rubbers, which make good "working joints," the
choice of which one to use depends on the by-products.
For example, ELASTOSIL® E43 would not be suitable for joining
two bits of marble as the acetic acid by-product would attack the marble
and impair the joint quality. |
 |
 4
Tips and Comments
|
 |
- The experiment can be speeded up by omitting
the “long-term” temperature measurements and
simply measuring the rise in temperature at the start of
curing.
This can be used to demonstrate that exothermic reactions
predominate during both curing of gypsum and curing of
silicones.
- The experiment
could be extended by studying the influence of atmospheric
moisture on curing. To do this, fill a further U-profile
with an RTV-1 silicone in parallel to the experiment above,
store in a desiccator over dry silica gel under a water-jet
vacuum.
Note that the time needed for curing increases. When this
experiment was performed on ELASTOSIL® N199, three days
were needed for curing, whereas only one day was needed when
it was performed
in air. Curing never fully failed to materialize. The reason
is that the water-jet pump cannot remove all the atmospheric
moisture, and curing only requires small amounts of water.
- Another
variant is to make an aquarium using RTV-1 silicone.
Make the aquarium by using ELASTOSIL® E43 or N199 to join
five grease-free glass plates (cleaned with acetone or
ethanol) at right angles to each other (photo 4). When curing
is complete,
test that it is leakproof. A similar experiment was very
successful, as seen in photo 4.
|
 |
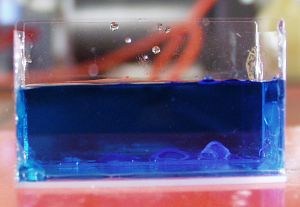 |
Photo 4: Glass plates bonded together
with ELASTOSIL® silicone |
 |
 5
Supplementary Information
|
 |
Room temperature curing, one-part silicone
rubbers, also known as RTV-1 grades (1-part room-temperature vulcanizing) already contain all the ingredients necessary
for curing, such as polyorganosiloxanes, crosslinkers and fillers.
The curing process, which releases by-products, only takes
place
on exposure to atmospheric moisture. RTV-1 silicone rubber
compounds are made by making hydroxy-terminated polysiloxane
molecules
react with crosslinkers to form curable products (see Fig.
2). |
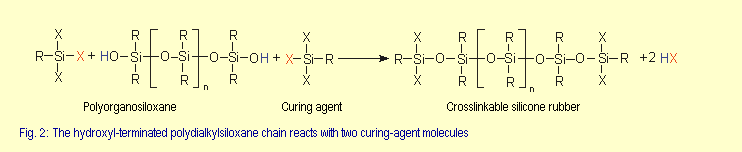 |
The standard base rubber compound is a polydimethylsiloxane
(R = CH3).
Table 2 shows the most common types of crosslinkers (RSiX3)
along with examples of the X group. |
 |
Type
of crosslinker |
X
group (Name) |
X
group (formula) |
Acidic |
Acetoxy |
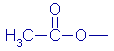 |
Octoate |
 |
Neutral |
Amide |
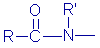 |
Oxime |
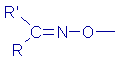 |
Alkoxy |
 |
Alkaline |
Amine |
 |
|
 |
Curing proceeds in the presence
of atmospheric moisture by the mechanism shown in Fig. 3. The
by-products vary with the type of crosslinker employed. Crosslinking
between silicone macromolecules occurs in subsequent reaction
stages and involves residual X groups. |
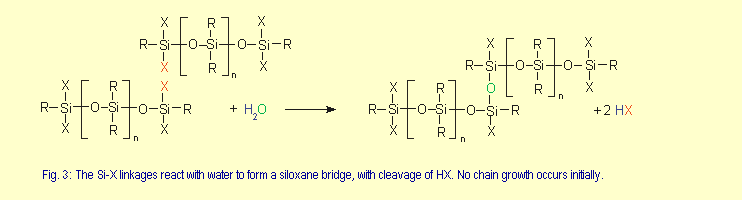 |
At the macroscopic level, curing starts on the surface of
the silicone rubber with the formation of a skin and gradually
works its way into the compound. Premature crosslinking is
prevented by the use of sealed packaging, such as tubes and
cartridges.
As shown in Fig. 4, the higher the content of moisture in the
air, the higher the curing rate.
|
 |
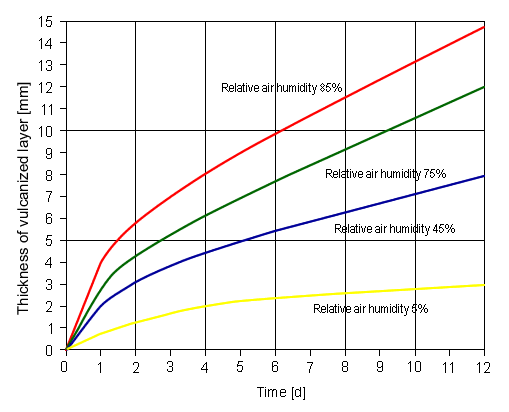 |
Fig. 4. Curing rate of ELASTOSIL®
as a function of atmospheric moisture at room temperature (Source:
Ref. [2]). |
 |
Like all silicones, RTV-1
silicone elastomers (the cured rubbers) are highly resistant
to chemicals,
ozone and UV radiation (see also experiments "Influence
of ozone on silicone rubber compared with other types of rubber" and "Solubility
and chemical resistance of silicone rubber"). They are
also noted for their outstanding water repellency. However,
the properties
of silicone elastomers vary according to the crosslinking systems
employed, and this determines their suitability for specific
applications. |
 |
Alkaline
systems |
Neutral
systems |
Acidic
systems |
|
No odor released
during curing |
|
|
|
Good adhesion to glass,
ceramics, metals and plastics |
Good adhesion to
building materials, glass, ceramics |
No corrosion of metals
or plastics |
|
Readily compounded (applies
to amine systems) |
|
Excellent transparency
(applies to acetoxy system) |
Good mechanical properties |
|
Good mechanical properties |
Environmental stress
cracking of polycarbonates |
|
Environmental stress
cracking of polycarbonates |
|
Table 3: Properties of various silicone
rubber elastomers made with different crosslinkers (Source:
Ref. [2]). |
 |
The aforementioned properties,
simplicity of use and reliability, make RTV-1 silicone elastomers
excellent sealant and jointing materials for avoiding stress
cracking in masonry. This is caused by constant movement and
stresses that result from thermal fluctuations, moisture-related
causes, shrinkage of building materials, mechanical fluctuations
or subsidence of the substrate. These deleterious effects can
be avoided by bridging the movements with elastic joints. This
is especially true for combinations of different materials, such
as glass/metal or stone/metal, because each one has a different
coefficient of expansion.
RTV-1 silicone rubbers are therefore mostly used in the construction
industry and are probably the silicone products best known to
the general public, especially the products sold in cartridges.
Other application areas are to be found in the automotive, electrical,
electronics and textile industries, where they serve as seals,
bonded joints and coatings. |
 |
 6
References |
 |
W. Held et al., Learning
by Doing – School Experiments with WACKER Products
(handbook accompanying WACKER's Experimental Kit), Wacker Chemie AG, Munich,
2007, p. 50-51 |
 |
|