1. Experiment is contained in the WACKER's Experimental Kit. |
No |
2. Experimental procedure has been modified |
/ |
3. A separate experimental procedure has been devised |
No |
4. Video clip available |
No |
5. Flash animation available |
No |
6. Other materials: "Ozone" on
the Wuppertal University “Didactics” homepage |
 |
Influence of Ozone on Silicone Rubber
and Other Types of Rubber |
 |
 1
Materials, Chemicals, Time Needed |
 |
- Ozone apparatus with UV lamp, available,
for example, from Hedinger, Stuttgart
- Aluminum foil
- Glass tube
- Glass rod
- 2 stoppers
- Wash bottle
- Spring balance
- Press
- Microscope
- Scotch tape
- Carpet knife
- Various rubber samples (bicycle inner tube, rubber tubing,
natural rubber)
- Various silicone rubber specimens from WACKER's Experimental Kit, e.g. HTV
- Oxygen, O
- Sulfuric acid, conc., C
Allow about 10 minutes to set up the apparatus.
It takes about 20 minutes to conduct the experiment, including
examining the specimens under the microscope. |
 |
 2
Procedure and Observations |
 |
First, set up the apparatus (see diagram). |
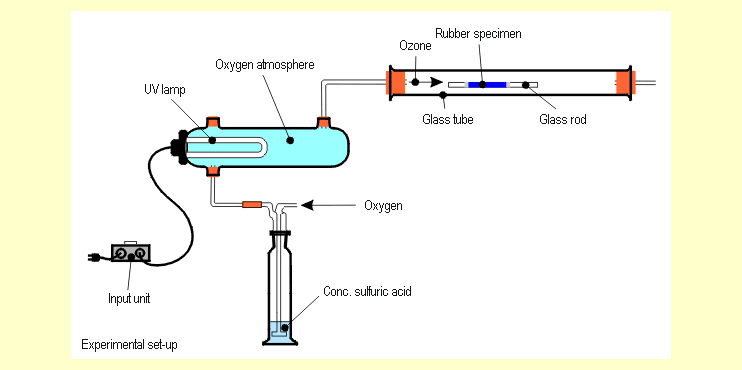 |
 As
ozone will be used, conduct the experiment in a fume cupboard.
Cover the ozone reactor with aluminum foil (protects against
UV radiation; see photo below).
Cut various rubber specimens into long rectangles of uniform
thickness and about 0.5 cm in width.
Clamp each rubber specimen lengthwise, ensuring it is held
adequately in the retort (see photo), and measure the elongation
under a force of 10 N.
Use Scotch tape to attach the specimen under the same elongation,
i.e. under a force of 10 N, to the glass rod and then place
this assembly face up in the glass tube (see diagram above).
Generate the ozone by first flushing the entire apparatus with
dry oxygen (see diagram above) for about 2 minutes. Then switch
on the the UV lamp and slowly (roughly 1 bubble per second)
pass the mixture of oxygen and ozone generated in the UV reactor
over the rubber specimen inside the glass tube. Continue the
ozone treatment for 15 minutes. Examine the specimen for macroscopic,
microscopic and mechanical changes.
It is important to ozonate all the specimens under the same
conditions in order that their resistance to ozone may be compared.
|
 |
The following reproducible observations
were made in reference experiments under an elongation of 10
N:
 Bicycle
inner tube (force = 10 N, width = approx. 0.5 cm)
Even as the ozone was being fed in, small cracks formed initially
in the surface of the specimen perpendicular to the acting force.
The cracks gradually grew until the rubber tore completely after
about 10 minutes.
A check of the mechanical properties revealed an extensive decline in tear strength
and elasticity.
Examination under the microscope after ozonation revealed small black veins (see
photos 1 and 2).
|
 |
 Rubber
tubing (force = 10 N, width = approx. 0.5 cm)
As with the bicycle inner tube, small cracks appeared first in the red
rubber tubing (laboratory tubing) and grew until the specimen eventually
tore after about 7 minutes.
Again, there was an extensive reduction in mechanical properties (tear
strength and elasticity).
After ozonation, red veins were seen under the microscope (see photos 3
and 4). |
 |
 Natural
rubber: (force = 1 N, width = approx. 0.5 cm)
The natural rubber specimen was only stretched under a tensile force of
1 N, as otherwise it would have become too long.
During ozonation, the specimen turned white or lost its transparency. Fringes
formed at the edge of the specimen. Small holes and cracks formed in the
center (see photo 5). After 10 to 15 minutes, the specimen tore at one
point.
Those areas of the specimen that lost their transparency were no longer
as elastic and tore faster.
Examination under the microscope after ozonation revealed small black dots
that were absent beforehand (see photos 6 and 7). |
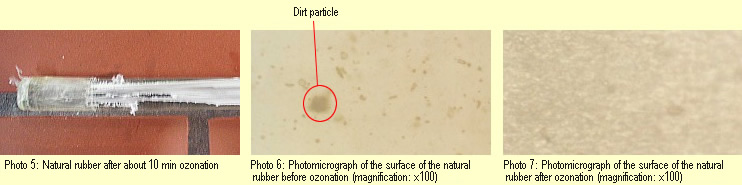 |
 Silicone
rubber HTV(b): (force = 10 N, width = approx. 0.5 cm)
Ozonation failed to produce any macroscopic (see photo 8), microscopic
or mechanical changes in the HTV(b) silicone rubber specimen from
WACKER's Experimental Kit. |
 |
Unfortunately, photographs could
not be taken under the reflected-light microscope as a sharp
image of the specimen could not be obtained. The specimen was
too thick for a transmitted-light microscope.
 Silicone
rubber HTV(s): (force = 10 N, width = approx. 0.5 cm)
Again, no macroscopic, microscopic (see photos 9 and 10) or mechanical
changes were observed.
|
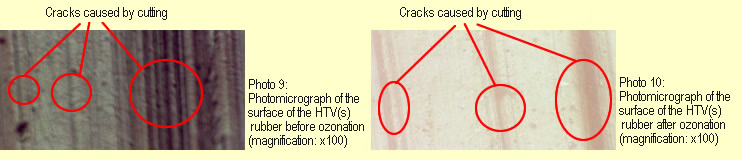 |
The differences in the appearance
of the photomicrographs are caused by different light intensities
when the photographs were taken. The clearly visible parallel
lines were caused by the carpet knife during cutting and not
by ozonation.
 Silicone
rubber HTV(w): (force = 10 N, width = 0.5 cm)
No macroscopic or mechanical changes were observed either before or
after ozonation.
As with silicone HTV(s), the slight differences in the photomicrographs
(see photos 11 and 12) may be explained in terms of differences in
light intensity during photography and the different structures created
by cutting. They are not due to ozonation.
|
 |
 |
 3
Discussion of Results
|
 |
From the observations above, it may be said that “silicone
rubber” (more accurately: the silicone rubbers from
WACKER's Experimental Kit) is not attacked by ozone under the conditions
of the experiment.
In contrast, “normal rubber” of the kind used in
rubber tubing (laboratory tubing), bicycle inner tubes and
natural rubber, is extensively attacked by ozone and is destroyed.
The order of ozone resistance is therefore as follows:

The “normal types of rubber” are attacked much
more extensively than the silicones because they are made
from polymers that contain carbon=carbon double bonds (C=C).
These
react with ozone (see below).
Silicone polymer molecules generally do not contain any carbon=carbon
double bonds and thus cannot be attacked by ozone. For example,
a 2 % content of ozone in the atmosphere will not bring about
any changes in the properties of silicone rubber, not even
for 70 hours exposure at 40 °C. Given natural
aging processes, silicone rubber is virtually totally resistant
to
oxygen and ozone.
 The
specimens in the experimental apparatus were exposed to ozone
concentrations that are much higher than occur naturally
(compare the ozone content of air in 5 Supplementary
information).
Despite its low concentration at the earth’s surface, ozone does still
play an important role in the atmospheric aging of plastics and elastomers. Ozone
causes aging in two different ways.
In saturated polymers, it initiates oxidation.
The free radicals formed at the start of the reaction then participate in further
reactions.
 |
 |
 |
Ozone plays a much more important role
in the degradation of polymers containing C=C double bonds
of the kind found in conventional rubber. Rubber is natural
rubber latex (cis-1,4-polyisoprene) that has been vulcanized
with sulfur. |
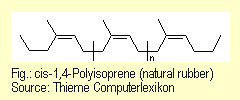 |
|
 When
ozone reacts with unsaturated compounds, the molecules are cleaved
at the C=C double bonds. For this reason, the reaction is also
called ozonolysis. Ozonolysis leads to oxidative degradation
of alkenes to carbonyl compounds, whose molecules contain fragments
of the alkene molecule.
The mechanism of ozonolysis involves electrophilic addition of
the ozone across the double bond. This transformation yields
the primary ozonide. The primary ozonide is unstable and fragments
into a carbonyl compound and a carbonyl oxide. Further reactions
then follow. |
 |
In the case of unsaturated polymers, such
as natural rubber (cis-1,4-polyisoprene), ozonolysis destroys
the polymer chains and thus changes the properties of the material.
The extent to which ozone affects unsaturated polymers, especially
natural rubber, depends on whether or not the polymers are being
subjected to mechanical stress at the same time. In the absence
of such stress (e.g. stretching and relaxation of a piece of
rubber), an ozonated layer builds up on the surface of the rubber,
forming a kind of protective barrier that prevents more ozone
from penetrating into the compound.
 Mechanical
stress (e.g. stretching or elongation) leads to the formation of typical
ozone cracks, with the cracks always occurring perpendicular to the acting
force.
One possible explanation for the accelerating effect of mechanical stress
on the degradation of elastomers by ozone is that the deformation mechanically
destroys the ozonated surface layer. This exposes fresh surfaces and facilitates
further reactions between the ozone and the elastomer.
Crack formation is a serious type of damage because, if the cracks grow as
degradation is happening, the product concerned may be totally destroyed.
Ozone cracking depends both on the composition of the rubber and on the mechanical
stress, ozone concentration and the temperature.
Ozone-induced changes in the polymer chain of the elastomer manifest
themselves as a reduction in tensile strength, extensibility and structural
strength. Furthermore, the oxidation generates functional groups containing
oxygen that reduce the mobility of the polymer chains and thereby impair
the material’s dynamic properties.
|
 |
 4
Tips and Comments
|
 |
- Since the tensile stress acting
on the specimens varies with the width and thickness of
the specimens, quantitative comparison is not possible. Simple
tools (e.g. carpet
knife) are unable to cut the specimens uniformly.
- The length of
time needed for the specimens to tear fluctuates in accordance
with the tensile stress, the ozone concentration,
the temperature and the degree of crosslinking.
- Except for
the temperature and possible tensile stress, these measuring
parameters cannot be kept constant. However, as
the observations show, this has no effect on the qualitative
results.
If the tensile stress is too low, the specimens show
no reaction.
- Since no changes were observed in the silicone specimens
at 10 N, the experiment was repeated on these specimens
by stretching
them as far as possible by hand. However, there were
no observable changes. Additionally, the silicones were placed
in an ozone
atmosphere (tube was sealed with Scotch tape) for longer
than a day. Again, there were no changes.
- The experiment
has a fairly high bearing on everyday life, because resistance
to ozone affects the scope for using
the elastomers
concerned and is thus regularly checked in industry.
- The
experiment can serve to familiarize the pupils with an
important property, namely the great difference between
the
resistance
of silicone rubber and other natural and synthetic
elastomers to ozone.
- This difference in materials can be graphically
illustrated at the particle level on the basis of the structural
feature of
the “C=C double bond”, even if the
mechanism of ozonolysis itself is not discussed.
It is enough
to restrict
the classroom
lesson to the overall reaction involved in ozonolysis.
|
 |
 5
Supplementary Information
|
 |
Ozone O3 is formed in the ozonosphere at a height
of 20 to 60 km above the earth’s surface by the following
photochemical reaction of oxygen at wavelengths less than 242
nm.

M represents a collision partner, e.g. a nitrogen or oxygen molecule,
which is needed to absorb the energy released.
Ozone formation is counteracted mainly by photolysis at longer wavelengths
to maintain a photostationary equilibrium between oxygen and ozone in
the ozonosphere.

The constant turbulence present causes some ozone to be transported by
airstreams down as far as the earth’s surface. Some of the ozone
in the lower layers of the atmosphere is also formed by electrical discharges
(lightning) and some ozone close to the ground is formed as photochemical
smog when intense sunlight acts on airborne impurities (vehicle exhaust
fumes).
Nevertheless, the average concentration of ozone at the earth’s
surface is very low. It varies from 0.02 ppm to 0.05 ppm as a function
of the season, the location of the measuring point and the meterological
conditions.
Further information (in German) on the subject of ozone may be found
under http://www.chemiedidaktik.uni-wuppertal.de/ > Unterrichtsmaterial > Ozon. |
 |
 6
References |
 |
- M. Tausch, M. von Wachtendonk (editors), CHEMIE S II, STOFF-FORMEL-UMWELT,
C.C. Buchner, Bamberg (1993), (1998), S. 226 f., S. 384 f
- M. Tausch, M. von Wachtendonk (editors), STOFF-CHEMIE S
I, FORMEL-UMWELT, C.C. Buchner, Bamberg (1996), (1997), S.
58 f
- M. Tausch, M. von Wachtendonk (editors), CHEMIE 2000+,
C.C. Buchner, Bamberg (2001), S. 78 f
|
 |
|
|