 |
Silicone-Coated Paper
 1
Materials, Chemicals, Time Needed
- Wooden board
- Paper
- Glass rod
- Drying cupboard or hot plate
- Scotch tape
(or other adhesive tape)
- Glass beaker, 100 ml
- DEHESIVE® 920, Xi, F, N
- WACKER Crosslinker V24, Xi, F, N
- WACKER Catalyst
OL, Xi
(See Part
5 Supplementary Information and References for details about abbreviations)
Allow around 45 minutes to prepare the DEHESIVE® mixture
and to coat the paper. The curing time depends on the temperature
and the coating thickness. However, it should be around 30
minutes max. at the temperature of the experiment. The experiment
can therefore be performed during a double lesson.
 2
Procedure and Observations
Add 1.3 g Crosslinker V24 (clear liquid)
to 50 g DEHESIVE® (clear liquid) and stir both
liquids with a glass rod. Add 0.5 g of Catalyst OL (yellowish
liquid) and then stir again vigorously. Coat the papers as
follows: |
 |
- Tape
the paper to the wooden board or other flat, solid washable
surface.
- Apply a bead of the reaction mixture to one end
of the sheet.
- Use
the glass rod to spread the mixture over the paper. Do
this by pressing the rod firmly onto the paper and drawing
it downward
(see photo, right).
- Then place the coated paper in the drying
cupboard at approx. 130 °C and measure how much time
elapses until curing is finished. When curing is finished,
the paper
will no longer be
tacky. Repeat the experiment to determine the curing time
at 50 °C and 100 °C.
- Finally, test the adhesive strength
of Scotch tape on the coated and uncoated paper.
When the reaction mixture is being prepared,
a clear, readily flowing liquid is formed (right) that is easy
to spread over the paper to be coated.
It cures in the drying cupboard to form a clear, smooth, glaze-like
coating on the paper.
 |
 |
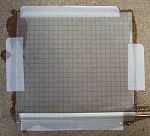

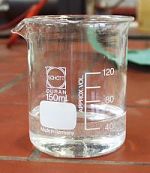
DEHESIVE® mixture |
 |
The following
observations may be made when comparing the adhesion of
strips of tape to coated and uncoated paper:
When the tape is removed from the untreated paper, the
paper is damaged. The tape has lost its tacky properties
and has become useless.
In contrast, the tape attached to the coated paper can,
just like sticky labels, be removed easily and without
damage, and can be reused (see photos below).
|
 |
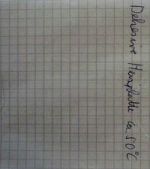 |
|
Paper coated with DEHESIVE® |
|
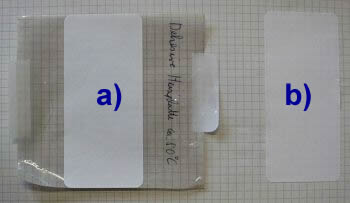 |
 |
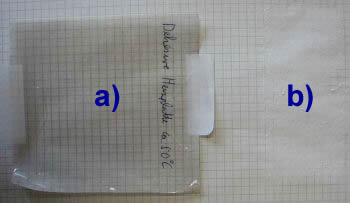 |
Strips of tape attached to siliconized
(a) and non-siliconized (b) paper |
|
Siliconized (a) and non-siliconized (b)
paper after the strips have been removed |
|
 |
The experiment to investigate the rate of
curing as a function of temperature shows that the curing time
depends heavily on the coating thickness and decreases with
increasing temperature. In several reference experiments, mean
curing times were measured as a function of the thickness of
the silicone coating and the temperature (see Table 1). |
 |
Temperature
in °C |
Curing
time in minutes |
130 |
Approx. 1 |
100 |
Approx. 3 |
50 |
Approx. 20 |
|
Table 1: Curing times
at different temperatueres |
 |
 3
Discussion of Results
The DEHESIVE® 920
silicone rubber used in the experiment consists of polydimethylsiloxane
molecules that have crosslinkable vinyl groups. These undergo
addition curing (see Part 5 Supplementary Information) to form
a strongly adhering layer of silicone rubber consisting of
DEHESIVE® 920 on the treated paper. The methyl groups
of the silicone molecules align themselves such that they are
pointing away from the surface. Adhesion between the strip
of tape and the siliconized paper surface is relatively weak
because the intermolecular forces bonding the aligned silicone
molecules on the paper to the molecules of the adhesive are
fairly weak. The strip of tape can be readily removed from
the surface, without loss of adhesion.
In contrast, strong interactions occur between the cellulose
molecules of the untreated paper surface and the molecules
of adhesive. Once the strip of tape has been removed, it cannot
be reused and the paper itself is damaged.
The rate of the addition-curing reaction is increased by raising
the temperature. The curing time therefore falls as the temperature
rises. |
 |
 4
Tips and Comments
- It is best to weigh out and prepare the mixture
in a glass beaker because the catalyst and crosslinking
agent are viscous. If they were transferred separately to
the beaker,
the amount transferred would not be the same as the amount
weighed out.
- Before heating, remove the paper from the wooden
surface as otherwise the curing time will be much longer.
The reason is
that the wood does not heat up as quickly as the paper
and tends to have a cooling effect.
- The curing time varies with
the layer thickness. Therefore, ensure that layers of
similar thickness are applied to the
paper. The temperature-dependence of the curing rate
can be readily observed despite different layer thicknesses.
However,
the curing times are less reproducible.
- If a drying cupboard
is not available, heat the pieces of paper on standard
hot plates. The results will be less accurate
because
the temperature cannot be set so precisely. The curing
times will also be different from those in the drying cupboard.
Nevertheless, the dependence of the curing time on the
temperature
is readily
observed. Several reference trials conducted at 50 °C
and 100 °C yielded the curing times shown in Table
2.
|
 |
Temperature in °C |
Curing time in minutes |
Approx. 100 |
Approx. 1 |
Approx. 50 |
Approx. 15 |
|
Table 2: Curing times
as measured with an electric hot plate |
 |
 5
Supplementary Information
DEHESIVE® silicone release
papers are widely used to cover and protect the adhesive on
sticky labels so that they will stick where they are supposed
to. In the experiment described, just as in practice, both
solvent-based and solventless addition-curing or condensation-curing
polydimethylsiloxanes (silicone rubber) are used for coating
purposes. These cure very quickly at temperatures of 100 – 200 °C.
Release papers generally are constructed as follows: |
 |
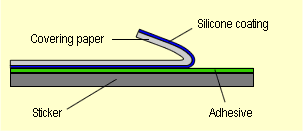 |
Fig. 1. Structure of
a pressure-sensitive adhesive with a silicone coating (Source:
Ref. [11], p. 40) |
 |
The application areas of silicone release
papers are shown below: |
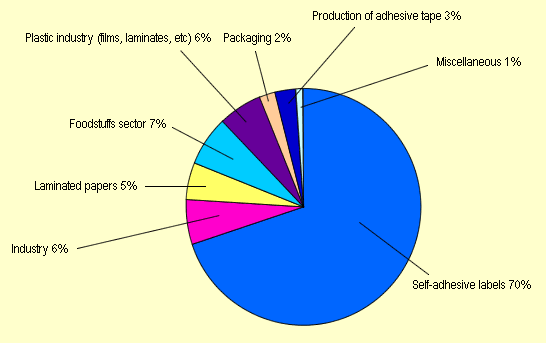 |
Fig. 2. Use of silicone
release papers (Source:
Ref. [11], p. 40) |
 |
To produce a very flexible, individual consistency
for different coatings, the DEHESIVE®- silicone
coating used in the experiment is generally processed in the
form of a 3-component material in practice.
These components
are:
- Polymer (DEHESIVE®):
Solvent-based and solventless polydimethylsiloxanes whose
end groups consist of crosslinkable hydroxyl or vinyl groups.
- Crosslinker: hydrogen polysiloxanes
with a high content of reactive Si-H groups for thermal hardening
of addition-curing systems. The nature and quantity of the
crosslinker determines the rub-off resistance and adhesive
strength of the silicone film.
- Catalyst: platinum
complexes (0.1 %, 1,000 ppm) for thermal curing of silicones.
The quantity of catalyst employed determines the production
rate, the curing temperature and the pot life (the maximum
length of time during which the mixture can still be used).
|
 |
The following reactions occur according
to the type of curing reaction: |
 |
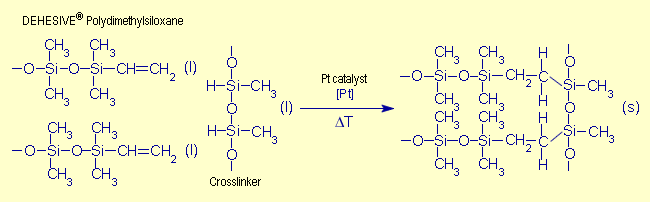 |
Fig. 3. Addition curing
of DEHESIVE® silicone rubber (Source:
Ref. [11], p. 41) |
 |
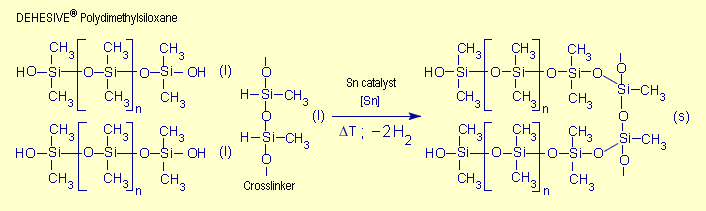 |
Fig. 4. Condensation
curing of DEHESIVE® silicone rubber (Source:
Ref. [11], p. 41) |
 |
In addition curing,
the hydrogen atoms from the Si-H groups add across the vinyl
groups of the polymers. Condensation curing also involves the
active Si-H groups from the crosslinking agent, but in this
case hydrogen is split off. In both cases, the silicone macromolecules
are linked together to form a network. The resultant material
adheres well to cellulose or glass, the polar sections of the
silicone molecules interacting (dipole-dipole and hydrogen
bonds) with the substrate. The methyl groups of the silicone
molecules project outwards (see also the experiment "Hydrophobic
properties of silicone fluids").
As a result, the silicone on the paper has a non-stick effect
or release effect on common adhesives, i.e. the adhesive either
bonds weakly or not at all to the silicone layer. This behavior
is due to the weak forces of interaction (Van der Waals) between
the molecules of the adhesive and the methyl groups of the silicone.
The unusually weak intermolecular bonding forces are also found
when the surface tension (surface energy) of silicones is compared
with that of other organic polymers, all of which have higher
surface energies (Table 3).
|
 |
Polymertyp |
Surface
tension in [mNm-1] |
Polydimethylsiloxane |
21-22 |
Polyphenylmethylsiloxane |
26 |
Polyvinylchloride |
40 |
Polyethylene |
30 |
Starch |
40 |
Wool |
45 |
|
Table 3: Surface tension
of various polymers (Source:
Ref. [2], p. 59) |
 |
 6
References |
|
W. Held et
al., Learning by Doing – School Experiments with WACKER
Products (handbook accompanying WACKER's Experimental Kit), Wacker Chemie AG,
Munich, 2007, p. 40 - 42 |
|