 |
 The GENIO Family: GENIOMER®, GENIOSIL®, GENIOPERL®
The GENIO family comprises hybrid products in which a silicone component is combined with another component to produce a material with customized properties.
GENIOMER® consists of linear macromolecules with organic and inorganic segments. In precise terms, it is a polydimethylsiloxane/urea copolymer. |
|
 All in all, this structure is responsible for an outstanding property profile that cannot be obtained either with standard thermoplastics or silicones alone. The soft silicone segment and the hard polyurea segment imbue GENIOMER® with elasticity and low-temperature flexibility on the one hand, and with strength and heat resistance on the other. GENIOMER® does not cure by forming covalent bonds but by forming physical hydrogen bonds between the urea segments. This reaction is reversible, with the material becoming plastic on heating and elastic on cooling. GENIOMER® requires no catalysts for curing, and it contains no plasticizers, fillers or other additives. It has a very long shelf life, is UV resistant, recyclable and has no known harmful effects. |
|
 Sheeting and hose made of GENIOMER® are produced by extrusion. On account of it’s hybrid structure, GENIOMER® is compatible with organic polymers and can hence be used, for example, to improve the flow properties of traditional thermoplastics such as polypropylene. The addition of 0.1 to 2 % GENIOMER® to polypropylene greatly increases its speed of processing. |
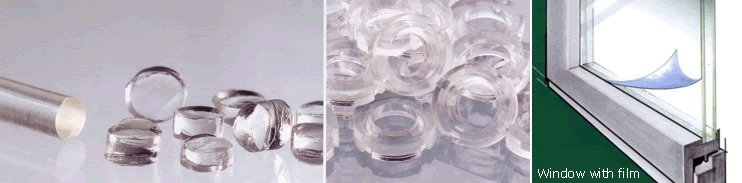 |
GENIOMER® is used in textile coating, the automotive and medical engineering sectors, and as a material for keyboards, dashboards, etc. in computers and other electronic equipment.
 GENIOSIL® is the name of a product family based on silicone macromolecules with terminal organofunctional silane units. In this case, these are alkoxysilane groups (e.g. trimethoxysilane groups, as in the formula below) that are separated from the silicone group by a methylene (-CH2-) bridge. They are known as α–silane building blocks.
|
|
On addition of water, these alkoxy groups hydrolyze very quickly. Subsequent condensation leads to rapid crosslinking of the silicone macromolecules. GENIOSIL® STP-E is an innovative material that functions according to this principle and produces very fast-curing, elastic adhesives. This α–silane technology based on the crosslinking principle described above is the key to a new generation of fast-curing, dimensionally stable installation foams that WACKER has made possible for the construction industry. Unlike traditional polyurethane foams, these foams are free of isocyanates. One example is Soudaform SMX®, which is just as effective as the familiar PU foam but complies much better with the new, stricter safety and environmental requirements. The conventional blowing agents propane and butane expand the GENIOSIL® silane foams, after which the foams remain dimensionally stable. The hardness of the white, water-repellent foams can be adjusted to requirements by varying the silane building blocks and by means of catalysts. Since the organofunctional α-silane groups react so readily with both inorganic and organic structural elements, GENIOSIL® is an excellent coupling agent. Various GENIOSIL® formulations accordingly find application in the manufacture of high-tech composites for the automotive and construction industries.
 GENIOPERL® is the name given to GENIO-family products consisting of tiny spheres with diameters of between 10 and 100 nm. The following diagram illustrates the production of these spherical particles comprising a silicone core and a polyacrylic or polystyrene shell that is just 100 to 200 atoms thick.
|
|
 In micelles of surfactant molecules, silane and siloxane molecules are hydrolyzed by water and converted into cross-linked silicones (1). Subsequently, polyacrylic or polystyrene chains form a shell around each of the silicone spheres (2). The surfactant molecules are then washed off the polymer shell (3). GENIOPERL® combines the properties of the two components that make up these nanoscale “bouncing balls.” Firstly, the silicone core makes them elastic, transparent, fracture proof and impact resistant over a wide temperature range from -40 °C to +250 °C. Secondly, thanks to the polymer shell, they can be modified such that they can be incorporated into a wide variety of substances. If GENIOPERL® is added to automotive paints, for example, it makes them glossy and impact resistant. The impact of small stones is cushioned, preventing the formation of scratches and holes in the paint. Small amounts of various substances with special properties, such as fluorescent pigments, photoreactive compounds or drugs, can be incorporated into the silicone core of GENIOPERL® nanospheres. Safely Inside their “GENIOPERL® containers,” these substances can then be incorporated into various materials or the bodies of patients. There, they are released again as they diffuse through the silicone network and the thin polymer skin. In the form of GENIOPERL®, silicones have become starters in the booming field of nanotechnology. They offer enormous potential, both for scientific research and for industrial investment. |
 |
|
|