 The
Müller-Rochow Synthesis of Chloromethylsilanes
Industrial synthesis of chloromethyl silanes
is almost exclusively carried out by the Müller-Rochow process.
In it, silicon is made to react with chloromethane. The reaction
proceeds under the catalytic influence of copper at temperatures
between 250 and 300 °C. The most important basic materials for
the production of silicones are sand, petroleum and salt.

For the conversion to be economical, the silicon
must meet certain requirements. It must be at least 97 % pure and
the particle size should lie between 45 and 250 µm. Purer silicon
would lead to more sluggish conversion rates while a purity level
less than 95 % would yield a raw silane mixture of unfavorable composition.
Overall,
the Müller-Rochow synthesis is very sensitive to foreign
metals. It responds best to copper. Too high a copper fraction
(between 20 % and 80 %) has a negative effect, though. While
the reaction
kick-starts very quickly, the silicon is consumed too quickly
and the conversion rate is poor. Even traces of other metals, such
as aluminum and lead, will lead to unwanted products. ZnCl2 and
ZnSO4 are added
in quantities of up to 0.2 % in an attempt to counteract this.
Their goal is to increase the activity and the selectivity of the
reaction. While traces of lead inhibit the reaction, antimony promotes
it and will accelerate the conversion of the reagents if
added in appropriate amounts.
 Some gases also influence the synthesis
by increasing the selectivity of the reaction. These include
HCl and H2.
The amount added determines whether the reaction mixture is
rich in halogens or poor in halogens.
The catalyst consists of either silicon-copper alloys or a
finely ground blend of the two metals. Precisely how the copper
works
is not known. However, it is generally assumed that the direct
synthesis
proceeds via the following intermediate state:
Since high space-time yields and high yields of
the target molecule dichlorodimethylsilane are only possible at temperatures
from 250 to 300 °C, and since the reaction is highly exothermic,
a close watch has to be kept on the temperature. It is controlled
by means of a cooling jacket over the reactor or by addition of inert
gas.
It is just as important to intimately mix the
catalyst in the stream of chloromethane. This prevents local overheating.
Nowadays,
fluid
bed reactors are used almost exclusively as they meet all these
processing requirements. The catalyst is placed in the reactor and
heated to
280 °C. A powerful stream of chloromethane is then introduced
at a tangent to cause turbulence. The turbulence caused by the gas
counteracts any tendency for hot spots to occur. Solid particles
can be separated off. At the end of the reactor, the raw silane mixture
is condensed to separate it from unreacted chloromethane. The silane
mixture is separated into its constituent silanes by means of column
distillation while the excess chloromethane is fed back into the
synthesis again.
 The
following diagram illustrates the Müller-Rochow process for
synthesizing silanes:
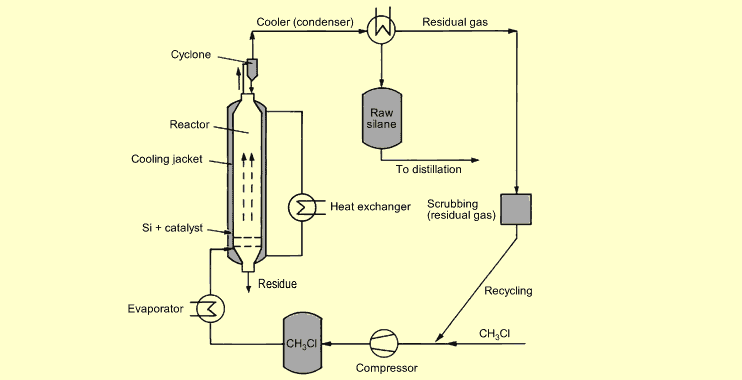
The most favorable pressure range for silane synthesis is 1 to 5
bar.
 Up
to 40,000 metric t/y of raw silane can be produced in modern fluid-bed
reactors. These silane mixtures have approximately the composition
shown in the following diagram:
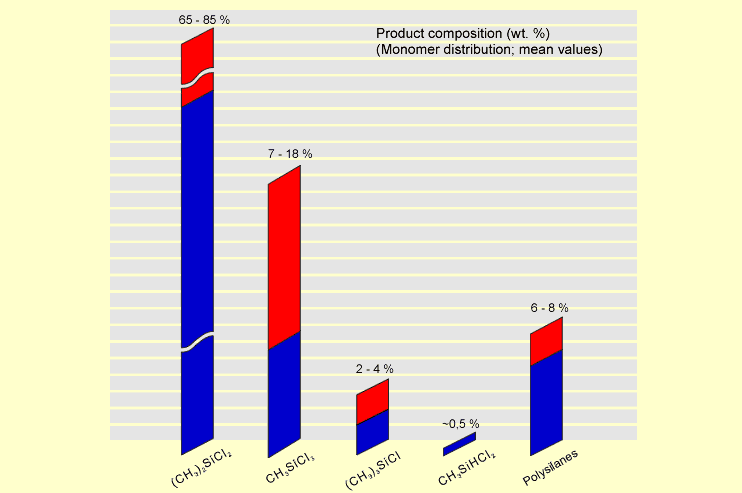
The raw silane mixture is purified by distillation
in a series of downstream columns. The purity of dichlorodimethylsilane
is critical. Even low fractions of trifunctional silanes would lead
to crosslinking reactions later. Fractions of monofunctional silanes
would have chain-terminating effects.
 The
following table provides an overview of the range of silanes that
occurs and their boiling points:
Name |
Formula |
Boiling point |
Chlorodimethylsilane |
(CH3)2HSiCl |
35 °C |
Dichloromethylsilane |
(CH3)HSiCl2 |
41 °C |
Chlorotrimethylsilane |
(CH3)3SiCl |
57 °C |
Trichloromethylsilane |
(CH3)SiCl3 |
66 °C |
Dichlorodimethylsilane |
(CH3)2SiCl2 |
70 °C |
Trichlorotrimethyldisilane |
(CH3)3Si2Cl3 |
152 - 156 °C |
Tetrachlorodimethyldisilane |
(CH3)2Si2Cl4 |
152 - 156 °C |
Tetrachlorosilane |
SiCl4 |
56.7 °C |
Higher silanes |
|
> 156 °C |
|
 |
The diagram at the left shows the typical structure
of a distillation column with bubble-cap trays (the diagram shows
a column for the fractionation of petroleum).
Silane distillation
requires columns with up to 200 trays and a reflux ratio
of 1:500. To avert the risk of water breakthrough,
they are air cooled.
Problems occur during the separation
of trichloromethylsilane from dichlorodimethylsilane since
the boiling points differ
only by 4 °C. To achieve the corresponding purity levels,
the first raw-silane distillation has to be followed by
a second
fine distillation.
Azeotropic mixtures of chlorotrimethylsilane
and tetrachlorosilane are also difficult to separate.
|
High-boiling by-products can be converted with
HCl under the catalytic influence of amines to the preferred product
dichlorodimethylsilane. Chloromethylsilanes can also be converted
to the desired dichlorodimethylsilane by treatment with AlCl3. Co-proportionation
occurs between (CH3)3SiCl and CH3SiCl3.
|