 |
Room Temperature Curing, Two-Part Silicone Rubbers |
 |
 1
Materials, Chemicals, Time Needed |
 |
- Balance
- 4 small glass beakers (it is best to use old beakers,
as the beakers are difficult to clean and a thin film
of silicone always remains behind)
- Various coins to act as patterns
(other objects could be used, too)
- 5 cardboard coffee cups
with flat bottoms
- Spatula
- Glass rod
- Drying oven
- Scissors
These three chemicals are contained in WACKER's Experimental Kit.
It takes about 15 minutes to prepare each
rubber compound. Curing times vary from 5 minutes at 150 °C
to several hours at 23 °C. The experiment therefore lasts
two days, although the actual time for the experiment is only
about 1 hour. The time needed for making a reproduction depends
on the material used for the reproduction. |
 |
 2
Procedure and Observations |
 |
ELASTOSIL® M 4601 moldmaking
compound is made by separately weighing out components M 4601
A and M 4601 B in the ratio
9:1 (by weight) and then mixing them until a uniform wine-red
color has been obtained.
To produce the ELASTOSIL® M 4400 moldmaking
compound, weigh out the requisite amount of ELASTOSIL® M
4400 (50.6 g was used in the reference experiment) and stir
in 2 to 3 wt % (1.3
g in reference experiment) of T 37. The result is a viscous,
yellow compound.
|
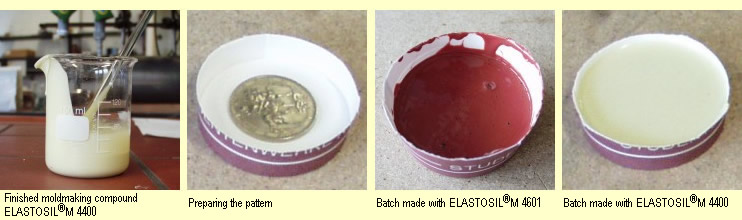 |
Trim the coffee cup in such
a way as to leave the base and a rim about 2 cm high. Place
the coin on the base of the cup and fill it to the rim with
the moldmaking compound. Prepare two cups in this way (three
in the case of ELASTOSIL® M 4400) for each moldmaking
compound. Cure one at about 100 °C in an oven and let the
second cure at room temperature. Let the third batch of ELASTOSIL® M
4400 cure at 55 °C in the oven.
Determine the weights of each before and after curing. Record
the amount of time needed for each compound to fully cure (curing
time). When curing is complete, remove the pattern (e.g. the
coin) and examine the silicone rubber mold (elasticity, appearance).
Use gypsum to make a positive mold of the pattern.
 Note
how the curing time of ELASTOSIL® M 4601 (addition-curing)
decreases rapidly with increase in temperature.
In contrast, ELASTOSIL® M 4400 (condensation-curing)
does not cure all at 100 °C. Although ELASTOSIL® M
4400 cures faster at 55 °C than at room temperature, curing
is not so dependent on the temperature as is the case for ELASTOSIL® M
4601.
The following results were obtained in a reference experiment: |
 |
|
ELASTOSIL® M
4601 |
ELASTOSIL® M
4400 |
|
25 °C |
103 °C |
25 °C |
55 °C |
103 °C |
Curing time |
1 day
(approx. 12 h)
|
Approx. 15 min |
1 day
(9 - 12 h)
|
Approx. 1 h |
No curing |
Weight before curing |
20.1 g |
27.4 |
24.0 g |
27.2 g |
/ |
Weight after curing |
20.1 g |
27.4 |
23.9 g |
27.1 g |
/ |
Loss in weight |
0 % |
0 % |
0.42 % |
0.36 % |
/ |
|
 |
 Both
types of curing yield highly accurate, bubble-free images of
the coins used. Both molds are elastic. Very accurate reproductions
of the coins can be made in gypsum. |
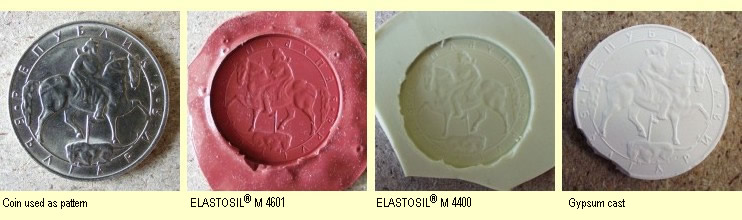 |
 |
 3
Discussion of Results
|
 |
The observations can be readily
explained in terms of the mechanisms for the two curing reactions
(see below).
RTV-2 silicone rubbers may undergo either condensation curing
or addition curing.
In condensation curing, a,w-dihydroxypolydimethylsiloxane
reacts reversibly with silicic acid esters in the presence of
catalysts such as dibutyl tin dilaurate or tin diacetate, releasing
ethanol in the process: |
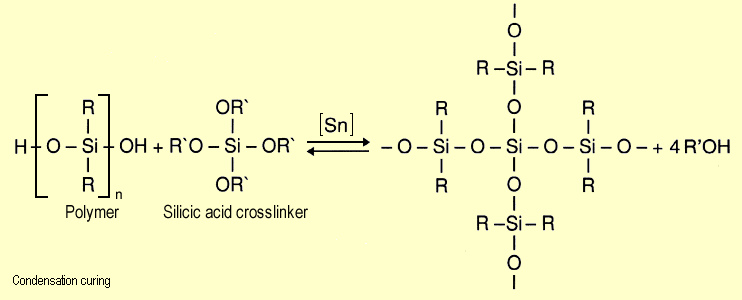 |
 Addition-curing,
by contrast, involves addition of Si-H across double bonds. The
catalysts employed here are salts and complexes of platinum (or
palladium or rhodium). If platinum-olefin complexes are used,
the reaction will occur at room temperature. Platinum-nitrogen
complexes require higher reaction temperatures. |
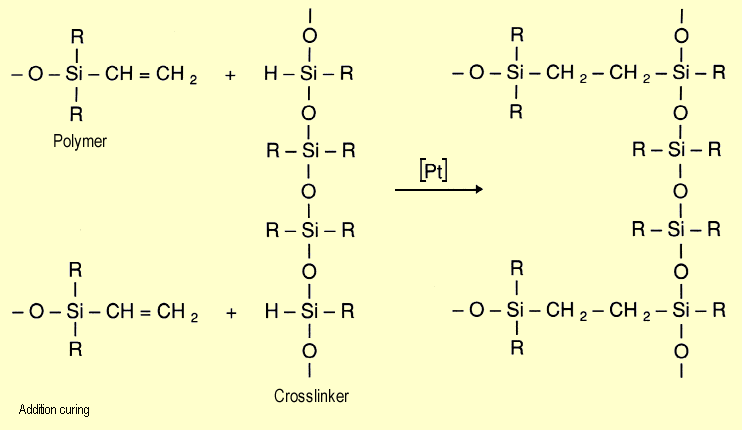 |
 The
key differences in the reaction conditions for the two types
of curing are shown in the following table. |
 |
Condensation
curing |
Addition
curing |
Blending ratio of
silicone rubber and catalyst variable within limits |
Blending ratio of
the two components is fixed |
The catalyst also
contains the crosslinker |
Crosslinker (H-siloxane)
present in rubber component A, catalyst in rubber component
B |
Curing impaired only
by lack of water |
Curing impaired by
different foreign substances (sulfur compounds etc) |
Curing rate largely
independent of temperature |
Curing rate heavily
dependent on temperature |
Chemical shrinkage
due to elimination of alcohol during curing |
Practically no shrinkage |
By-products (alcohol)
may cause depolymerization from 80 °C and above |
No depolymerization
possible |
Long pot life and
hence long curing times |
Where pot life is
long, curing can be accelerated by exposure to high temperatures |
|
(This table was compiled from Ref.
[2], p 48. |
 |
The condensation reaction releases
alcohol, which evaporates. The mold therefore shrinks during
curing and there is a loss in weight.
Condensation curing is an equilibrium reaction. From 80 °C
on, the equilibrium lies on the left and the curing reaction
starts to reverse (depolymerization). The system remains tacky
and liquid.
Addition curing does not generate any by-products. There is therefore
no reduction in weight observed. The reaction is irreversible.
Elevating the temperature in both types of curing reaction increases
the reaction rate and hence the curing rate. Raising the temperature
of ELASTOSIL® M 4601 has a greater effect on the
reaction rate than in the case of ELASTOSIL® M
4400. This difference is due to the different reaction mechanisms.
The elasticity of the two types of silicone rubber may be explained
by the crosslinks that form between the silicone macromolecules. |
 |
 4
Tips and Comments
|
 |
- Bubbling that may occur when gypsum is cast in new molds
can be prevented by treating the mold with soap beforehand.
- Experiments
to make reproductions in tin were unsuccessful because
ELASTOSIL® M
4400 is unstable at the melting point of tin and reverts
to being tacky. ELASTOSIL® M 4601, however,
remains stable. Nonetheless, even it failed to yield satisfactory
reproductions, all of which contained air bubbles.
- This experiment
can serve to illustrate the principle of curing in the
manufacture of silicone rubber and the reproduction
of objects. Comparison with vulcanization of natural rubber
is also conceivable.
- The pupils will not be able to work
out the reaction equations directly from the experimental
results. However, if the teacher
provides them, it should be possible for the pupils to
understand them since condensation and addition reactions
are covered
in the lesson. The knowledge gained about these two types
of reactions from other example reactions can be applied
to the
preparation of silicone elastomers.
- Since the experiment
is safe and simple, it is ideal for the classroom. It is
advisable to perform the experiment
in groups,
with one group using ELASTOSIL® M 4400,
and the other using ELASTOSIL® M 4601.
|
 |
 5
Supplementary Information
|
 |
 |
The elastic properties of elastomers
stem from a few crosslinks between the molecular chains
(see structural diagram). These crosslinks are generated
by crosslinking reactions between the macromolecules.
Natural rubber (cis-1,4-polyisoprene) is crosslinked by
sulfur at 150 °C. Bridges are formed that consist of
several sulfur atoms linking the polyisoprene molecules
to each other. Crosslinking is also known as vulcanizing. |
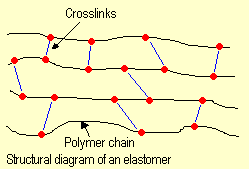 |
|
 |
 |
Certain silicone polymers, called silicone rubbers,
can also be crosslinked to form silicone elastomers.
Chemically speaking, silicone rubbers are linear silicone
polymers containing hydroxyl, vinyl or other reactive
groups. A silicone molecule containing vinyl groups is
shown on the right. These polymers can be crosslinked
in various ways at room temperature or higher temperatures
to yield wide-mesh structures that are extremely elastic.
This experiment uses two-component room-temperature-vulcanizing
silicone rubbers, also known as RTV-2 silicone
rubbers.
Silicone rubbers have several special properties. Chief
among these are:
- Flexibility largely unaffected by changes
in temperature
- Great resistance to heat and cold
- Mechanical properties
only slightly affected by changes in temperature
- Flame
resistance
- Electrical insulation
- High chemical and oil resistance
- Non-stick properties,
i.e. high release action
Gas permeability
- Good damping properties for shock and
noise
- Compounding versatility, i.e. organic substituents
can be varied
|
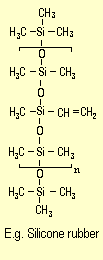
|
|
 |
 6
References |
 |
A. Tomanek: Silicones & Industry,
A Compendium for Practical Use, Instruction and Reference, Hanser,
Munich, Vienna (1990) |
 |
|