 Silicone
Rubber – Elastic, Flame-Fesistant, Oil-Resistant
First, typical structures of various silicone
rubber grades are shown, as described in more detail under "Manufacture".
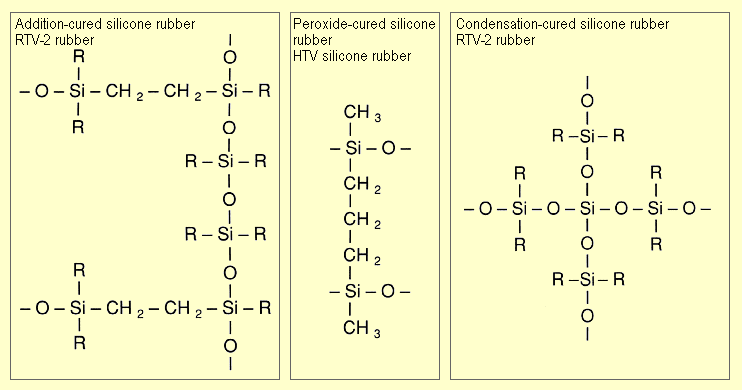
Several properties of silicone rubber will now be discussed
below.
 Elastic
Behavior
The best way to assess the elastic properties
of a material is to examine its stress-strain diagram. The
elastic modulus is a key parameter for describing elastic behavior.
It is given by the stress-strain curve as the resistance during
strain deformation (N/mm2) expressed in terms of a certain
strain value (in %).
A typical stress-strain diagram is shown
below.
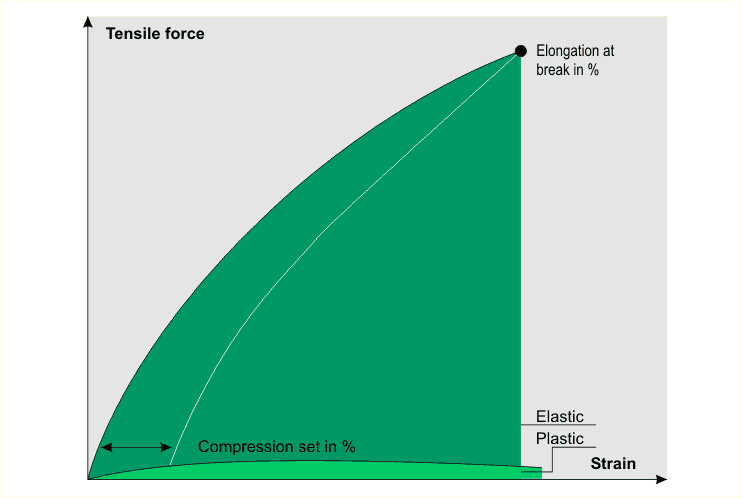
Silicone rubber possesses an extraordinary
property that sets it apart from other elastomers – its
elastic behavior changes only slightly with change in temperature.
 Compression
set of silicone rubber after 24 hours compression at
different temperatures:
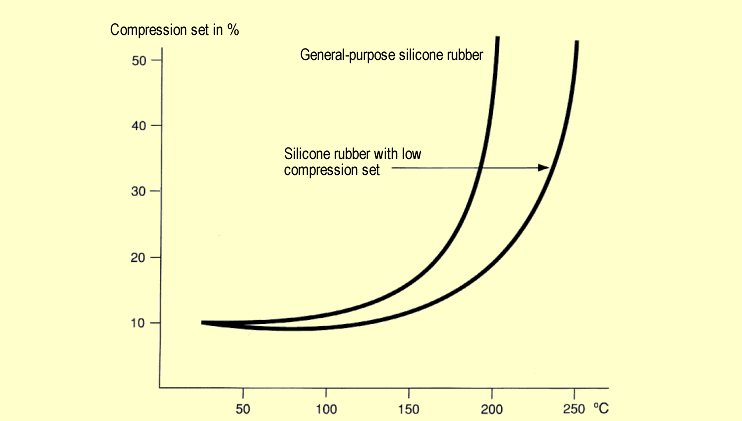
 The
following diagram shows the extent to which the crosslinking
density of the silicone rubber affects the different elastic
properties:
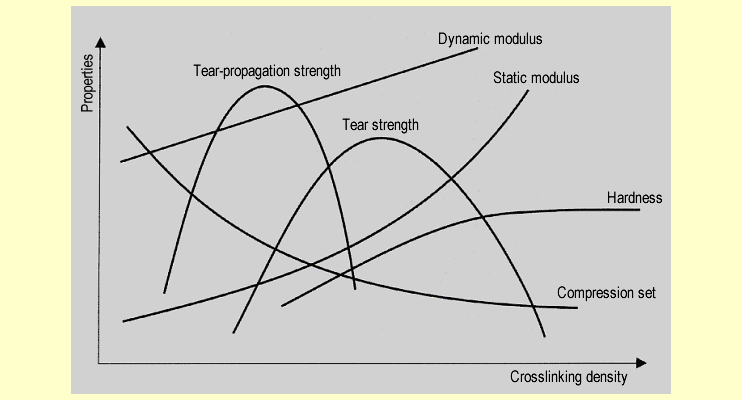
Of all the properties shown above, the most
important is the low dependence of the compression set on changes
in temperature.
 Flame
Resistance
Silicone rubber has excellent flame resistance.
It has a flash point of 750 °C, an ignition temperature
of 450 °C and its LOI values lie well below the critical
value of 21 % that approximates the concentration of oxygen
in air. (LOI is the abbreviation for limiting oxygen index,
which is a measure of the flammability of polymers in oxygen/nitrogen
mixtures of different composition).
Only very minor amounts
of smoke are evolved during combustion, and no toxic gases
such as HCl or sulfur compounds are released.

The principal combustion products are carbon
dioxide and water, with the ash consisting of silicon dioxide.
Since silicon dioxide is an excellent dielectric, silicone
rubber is used in critical sectors to sheathe cables (siliconized
cables are employed in shipbuilding, aircraft construction
and public buildings).
 To
emphasise the extremely positive properties of silicone rubber
in the event of fire, the combustion behavior of several elastomers
is tabulated below.
Polymer |
LOI % |
Smoke
density |
Fire load
[MJ/kg] |
Polychloroprene (CR) |
36.5 |
65 |
20.9 |
Chlorosulfate polyethylene
(CSP) |
30.7 |
85 |
15.9 |
Nitrile/PVC blend (NBR/PVC) |
30.6 |
136 |
20.5 |
Silicone rubber (VMQ) |
26 - 42 |
45 |
15.9 |
Styrene/butadiene rubber
(SBR) |
21.6 |
265 |
17.6 |
Ethylene/propylene
terpolymer (EPR) |
23.5 |
280 |
36.0 |
Chemically crosslinked
polyethylene (XLPE) |
20 |
205 |
41.9 |
Polyvinyl chloride
(PVC) |
24.3 |
265 |
22.2 |

Particularly flame-resistant grades of silicone rubber are made by incorporating
additives such as Al(OH)3 hydrate or minute amounts of
platinum compounds and TiO2 (for self-extinguishing products).
 Chemical
and Oil Resistance
Silicone rubber is generally very resistant
to chemicals. It can be used in applications involving contact
with dilute acids and alkalies. However, its chemical resistance
can decrease with increase in temperature or concentration.
Its
resistance to various oils compares very favorably with that
of organic elastomers. The following diagram illustrates
how the volume of silicone rubber changes when it has been
immersed at 150 °C in hot oil for 14 days or exposed to
other chemicals.
Chemicals |
Volume change in % |
 |
Solvents
and fuels (after 7 days at RT) |
|
Acetone |
15 - 25 |
|
Carbon tetrachloride |
Over 150 |
|
Ethyl alcohol |
0 - 10 |
|
Iso-octane |
Over 150 |
|
Xylene |
Over 150 |
|
Oils
(after 14 days at 150 °C) |
|
ASTM Oil 1 |
5 |
|
ASTM Oil 2 |
8 |
|
ASTM Oil 3 |
40 |
|
SAE Oil 20 W 20 |
25 |
|
Silicone fluid, viscosity
100 mPa s |
30 |
|
 |
 |
 |
Decomposed, aggressive oil components do
the most damage to silicone rubber. Nonpolar solvents, by contrast,
cause extensive swelling. However, the original properties
are restored when the solvent has evaporated. Silicone fluids
also cause reversible swelling of silicone rubber, with the
least swelling effected by the phenyl grades.
In contrast, silicone
rubbers containing trifluoropropyl groups are extremely resistant
to oil. |